Efficient warehouse management is crucial for e-commerce success. It ensures smooth operations and happy customers.
E-commerce businesses face unique challenges in managing their warehouses. From inventory control to order fulfillment, every step must be precise. Poor warehouse management can lead to delays, lost items, and unhappy customers. In the fast-paced world of online shopping, these issues can hurt your business.
Optimizing your warehouse processes can boost efficiency and customer satisfaction. It can also reduce costs and improve profitability. Whether you are just starting or looking to improve, effective warehouse management is key. In this blog, we’ll share practical tips to streamline your warehouse operations. Let’s dive in and explore how you can enhance your e-commerce business through better warehouse management.
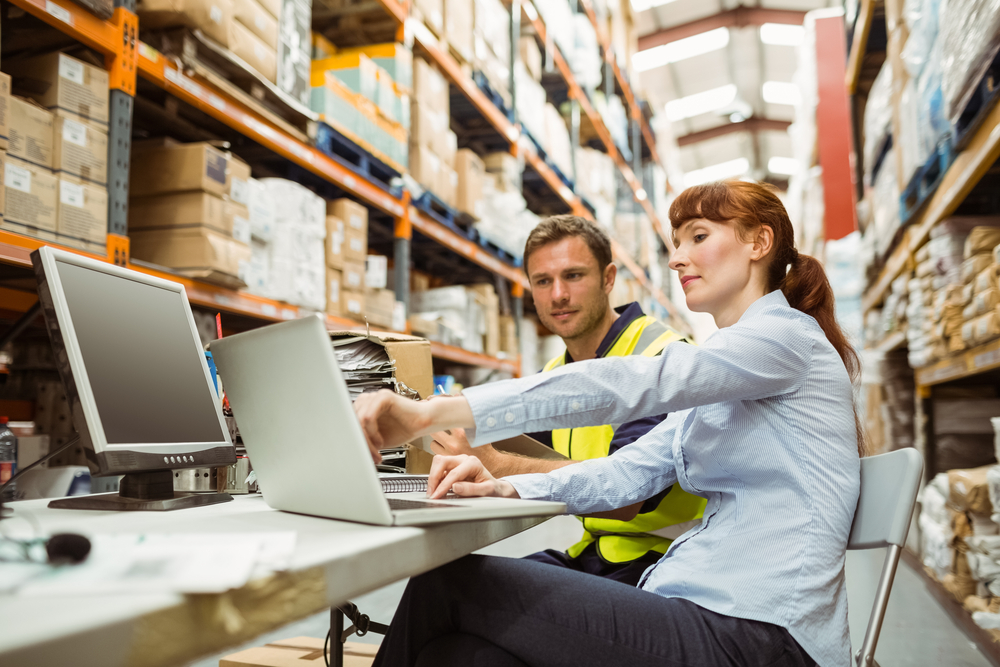
Credit: blog.shift4shop.com
Optimizing Warehouse Layout
Optimizing the layout of your warehouse can improve efficiency and save time. A well-organized warehouse reduces errors and speeds up order fulfillment. This section will cover practical tips for designing efficient pathways and organizing inventory zones.
Designing Efficient Pathways
Start by mapping out the main routes in your warehouse. Ensure pathways are wide enough for equipment and staff movement. Clear and direct routes reduce travel time and avoid congestion.
Place frequently picked items close to packing stations. This minimizes the distance staff need to travel. It also speeds up the picking process.
Use signs and floor markings to guide staff. Clear signage helps new employees navigate easily. It also enhances safety by marking hazardous areas.
Organizing Inventory Zones
Divide your warehouse into zones based on product types. Group similar items together for easy access. This can also simplify stock counting and inventory management.
Create distinct areas for fast-moving and slow-moving goods. Keep high-demand products near packing zones. Store less frequently picked items further away.
Label each zone clearly. Use large, readable labels. This helps staff find items quickly and reduces mistakes.
Consider using racks and shelves to maximize vertical space. This allows you to store more products without cluttering the floor.

Credit: www.youtube.com
Implementing Technology Solutions
In today’s fast-paced e-commerce world, staying competitive means optimizing every aspect of your operations. One of the most critical areas is warehouse management. Implementing technology solutions can significantly improve efficiency, reduce errors, and ultimately boost your bottom line. Let’s dive into some essential tips for leveraging technology in your warehouse management.
Using Warehouse Management Systems
A Warehouse Management System (WMS) is a game-changer for e-commerce businesses. It helps you keep track of inventory, manage order fulfillment, and streamline processes. With a WMS, you can:
- Automate inventory tracking and updates
- Optimize storage space and product placement
- Reduce human errors in order picking and packing
Imagine you run a small online store selling handmade crafts. Without a WMS, you might struggle with knowing exactly how much stock you have, where it’s stored, or which orders need to be fulfilled first. But with a WMS, all this information is at your fingertips, making your life a lot easier and your business more efficient.
Leveraging Automation
Automation can take your warehouse operations to the next level. By automating repetitive tasks, you free up time for your team to focus on more valuable activities. Here are some ways to leverage automation:
- Automated Picking Systems: Use robots or automated conveyor belts to pick products from shelves, reducing the risk of errors and speeding up the process.
- Automated Packaging: Implement machines that can package products quickly and accurately, ensuring consistency and reducing waste.
- Automated Inventory Replenishment: Set up systems that automatically reorder stock when levels drop below a certain threshold, preventing stockouts and overstocking.
Think about it this way: If you could have a robot do all the heavy lifting, why wouldn’t you? Automation allows your team to work smarter, not harder, ensuring that your customers get their orders quickly and accurately.
In conclusion, implementing technology solutions in your warehouse can transform your e-commerce business. By using a WMS and leveraging automation, you can streamline operations, reduce errors, and improve customer satisfaction. Don’t let your competitors leave you in the dust – embrace technology and watch your business thrive!
Streamlining Inventory Management
Effective inventory management is the backbone of any successful e-commerce business. When you streamline your inventory management, you ensure that your products are always available, minimize the risk of overstocking, and improve overall customer satisfaction. Now, let’s dive into some actionable tips under the subheading of Streamlining Inventory Management.
Implementing Real-time Tracking
Real-time tracking is a game-changer in inventory management. Imagine knowing exactly how many units of a product you have at any given moment. This can help you avoid the dreaded “out of stock” scenario. By implementing real-time tracking, you can:
- Reduce errors: Automated systems are less prone to mistakes compared to manual tracking.
- Improve accuracy: You’ll know precisely how much stock you have, which helps in making informed decisions.
- Enhance customer satisfaction: Customers get what they want, when they want it, leading to better reviews and repeat business.
Real-time tracking can be implemented using barcodes or RFID tags. These technologies allow you to update inventory levels instantly as items are received, moved, or shipped. Trust me, once you go real-time, you’ll never look back!
Conducting Regular Audits
Regular audits are essential to ensure your inventory records match the physical stock. While it might sound like a chore, it’s crucial for maintaining accuracy. Here’s how you can make the audit process smoother:
- Schedule audits regularly: Set a calendar reminder for monthly or quarterly audits.
- Use technology: Utilize inventory management software to track discrepancies.
- Train staff: Ensure your team knows how to conduct audits and understand their importance.
By conducting regular audits, you can:
- Identify discrepancies: Catch errors early before they affect your business.
- Prevent theft: Regular checks deter potential theft and maintain integrity.
- Maintain financial accuracy: Accurate inventory records are crucial for financial reporting and planning.
Think of audits as a health check-up for your inventory. They might not be fun, but they’re necessary to keep things running smoothly.
In conclusion, streamlining inventory management is not just about having the right amount of stock. It’s about ensuring accuracy, improving efficiency, and ultimately, making your customers happy. By implementing real-time tracking and conducting regular audits, you can keep your inventory in check and your business on the path to success. So, why not give these tips a try? Your future self will thank you!
Enhancing Order Fulfillment
Enhancing order fulfillment is a critical aspect of warehouse management for e-commerce businesses. Efficient and effective order fulfillment ensures customer satisfaction and repeat business. But how do you take your order fulfillment process from good to great? Let’s explore some practical tips and strategies to enhance this crucial part of your e-commerce operations.
Improving Picking And Packing
Picking and packing can make or break your order fulfillment process. Here are some tips to streamline these tasks:
- Organize Your Warehouse: Keep frequently ordered items close to the packing station. This reduces time spent moving around.
- Use Picking Lists: Provide workers with clear picking lists to avoid confusion and mistakes.
- Implement Batch Picking: Instead of picking one order at a time, pick multiple orders in one go. This boosts efficiency.
- Train Your Staff: Well-trained staff are faster and more accurate. Invest in regular training sessions.
Utilizing Barcode Systems
Barcode systems are a game-changer for e-commerce warehouses. Here’s how they can help:
- Reduce Errors: Scanning barcodes minimizes human errors compared to manual entry.
- Speed Up Processes: Barcode scanning is quick and easy, speeding up picking and packing times.
- Improve Inventory Management: Barcodes provide real-time updates on inventory levels, helping you avoid stockouts or overstocking.
- Enhance Tracking: Barcodes allow you to track items throughout the warehouse, improving accuracy and accountability.
Imagine this scenario: You receive an urgent order. With a well-organized warehouse and barcode system, you quickly locate the item, scan it, and pack it within minutes. The customer is thrilled with the fast delivery, and you earn a loyal customer.
To sum up, enhancing order fulfillment involves focusing on key areas like picking and packing and utilizing barcode systems. By implementing these tips, you can improve efficiency, reduce errors, and ultimately provide a better experience for your customers.
Training And Managing Staff
Effective training and management of staff are crucial for e-commerce warehouse success. Well-trained staff ensure smooth operations and better productivity. Proper management also boosts employee morale and reduces turnover.
Providing Comprehensive Training
Start by providing detailed training sessions for new hires. Cover basic warehouse operations and specific job roles. Use visual aids and hands-on practice to enhance understanding. Regular refresher courses keep everyone updated on new procedures.
Encourage experienced staff to mentor new employees. This promotes a collaborative work environment. Offer cross-training opportunities to make your workforce versatile. This helps manage workload during peak times.
Ensuring Safety Protocols
Safety should be a top priority in your warehouse. Begin with training on safety protocols. Teach staff about proper lifting techniques and equipment handling. Conduct regular safety drills to prepare for emergencies.
Provide personal protective equipment (PPE) and ensure its proper use. Display safety signs and guidelines prominently in the warehouse. Regularly inspect equipment to prevent accidents. A safe workplace increases productivity and reduces downtime.

Credit: virtina.com
Implementing Quality Control
Implementing quality control is vital for e-commerce businesses. It ensures that customers receive products that meet their expectations. This builds trust and reduces the chances of returns. A robust quality control process helps in maintaining high standards and customer satisfaction.
Conducting Inspections
Regular inspections of inventory are crucial. Check products for defects before shipping. This can prevent customers from receiving faulty items. Use a checklist for inspections. It helps in identifying issues quickly. Train staff to spot potential problems. This makes the inspection process more efficient.
Managing Returns Efficiently
Handling returns can be challenging. It is essential to have a clear process. Make it easy for customers to return products. Inspect returned items as soon as they arrive. Determine if they can be resold or need repair. This speeds up the process and reduces losses. Keep a record of returns. Analyze the data to find common issues. This can help improve the quality of future shipments.
Reducing Operational Costs
Running an e-commerce business comes with its own set of unique challenges. One major hurdle is keeping operational costs low while maintaining efficiency. Effective warehouse management plays a crucial role in this. In this section, we will discuss some practical tips on reducing operational costs in your warehouse. By focusing on optimizing space utilization and reducing waste, you can streamline operations and save money. Let’s dive in!
Optimizing Space Utilization
One of the easiest ways to reduce costs is to make the best use of your warehouse space. Think of your warehouse as a game of Tetris – you want to fit everything in the most efficient way possible. Here are some tips:
- Use Vertical Space: Don’t just focus on the floor. Use tall shelves and mezzanines to store items vertically. This maximizes your storage capacity without needing more floor space.
- Implement an Efficient Layout: Arrange your warehouse in a way that reduces travel time for your workers. Keep frequently picked items near the packing area and group similar items together.
- Invest in Racking Systems: Quality racking can help you store items securely and efficiently. Adjustable racks can be customized to fit different sizes of products.
- Regular Audits: Conduct regular audits to ensure that space is being used efficiently. This helps in identifying underutilized areas and making necessary adjustments.
Reducing Waste
Waste not, want not. Reducing waste in your warehouse can lead to significant cost savings. Here’s how:
- Minimize Packaging Waste: Use the right amount of packaging material. Over-packaging not only wastes materials but also increases shipping costs. Consider using reusable packaging.
- Reduce Product Damage: Handle products carefully and store them properly to prevent damage. Damaged goods result in waste and increased costs.
- Efficient Inventory Management: Overordering leads to excess stock which may become obsolete. Use inventory management software to keep track of stock levels and avoid overstocking.
- Recycle and Reuse: Set up a recycling program for cardboard, plastic, and other materials. Reusing packaging materials can also help in cutting down costs.
By focusing on optimizing space utilization and reducing waste, you can significantly lower your operational costs. Not only does this make your business more efficient, but it also helps you stay competitive in the fast-paced world of e-commerce. Got any personal tips or anecdotes on managing warehouse costs? Share them in the comments below!
Planning For Seasonal Demand
As an e-commerce business owner, you probably know that sales fluctuate throughout the year. Seasonal demand can turn your warehouse into a whirlwind of activity. To stay ahead, you must plan for these peaks. Proper planning ensures you meet customer expectations without breaking a sweat. Let’s dive into some actionable tips for navigating these busy periods.
Preparing For Peak Times
Think of your warehouse as a bustling beehive during peak seasons. To keep everything running smoothly, you need to be well-prepared. Here are a few steps to get ready:
- Forecast Demand: Analyze past sales data to predict future trends. Holidays, festivals, and special events are key indicators.
- Stock Up: Order extra inventory ahead of peak times. Nothing is worse than running out of popular items during a rush.
- Optimize Layout: Arrange your warehouse so that high-demand items are easy to access. This reduces picking time and speeds up the process.
Adjusting Staffing Levels
Managing a warehouse during peak times isn’t a one-person job. You’ll need extra hands to keep up with increased orders. Here’s how to adjust your staffing levels to meet demand:
- Hire Seasonal Workers: Bring in temporary staff to handle the surge. Make sure they’re trained and ready to go.
- Flexible Schedules: Allow your regular employees to work extra shifts. This can help cover peak periods without the need for permanent hires.
- Cross-Training: Train employees in multiple roles. This ensures you have a versatile team that can step in wherever needed.
By preparing for peak times and adjusting your staffing levels, you can handle seasonal demand like a pro. Remember, a well-planned warehouse is a happy warehouse. So, roll up your sleeves and get ready for those busy seasons ahead!
Frequently Asked Questions
How To Manage An E-commerce Warehouse?
Optimize inventory management, streamline order processing, use warehouse management software, train staff effectively, and maintain a clean, organized space.
What Is The Role Of E Commerce In Warehouse Management?
E-commerce enhances warehouse management by optimizing inventory tracking, streamlining order processing, and improving storage efficiency. Real-time data ensures accurate stock levels and quick order fulfillment. Efficient management reduces costs and increases customer satisfaction.
What Are The 5s Principles Of Warehouse Management?
The 5S principles of warehouse management are Sort, Set in Order, Shine, Standardize, and Sustain. These principles help maintain organization, improve efficiency, and ensure a safe working environment. Consistently applying 5S principles leads to streamlined operations and better inventory control.
How Does E-commerce Facilitate Better Inventory Management?
E-commerce uses real-time data to track inventory levels, reducing overstock and stockouts. Automated systems streamline inventory management, improving accuracy and efficiency.
Conclusion
Efficient warehouse management boosts e-commerce success. Organized inventory saves time. Proper labeling prevents errors. Regular audits ensure accuracy. Staff training enhances productivity. Utilizing technology streamlines operations. Prioritize safety for a smooth workflow. Implement these tips for better results. With focus and dedication, your e-commerce business will thrive.